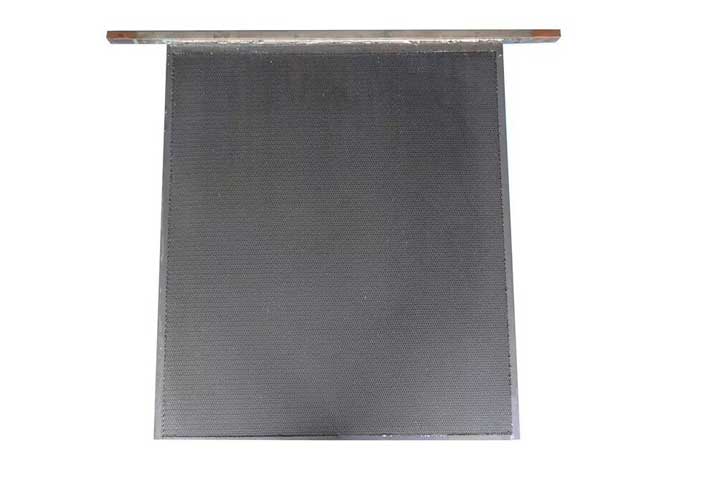
recovery copper titanium anode
Substrate: Titanium Grade 1 Sheet
Coating: Ir-Ta-X
Current density: Current density: 200-500A/m²
PCB industry production process produces a large number of micro-etching solution, etching solution, copper nitrate containing different concentrations of copper and other metals, high recovery value, and there will be a small amount of copper heavy metals in the effluent, such as can not be reasonable environmental protection treatment, on the one hand, resulting in a serious waste of resources, on the other hand, heavy metal emissions seeped into the soil and water, that is, we rely on the natural environment and their own health The pollution and harm will be serious.
Micro-etching solution
Microetching solution includes sodium persulfate/sulfuric acid system and hydrogen peroxide/sulfuric acid system, which are widely used in PCB surface treatment process in recent years, such as: copper sinking (PTH) process, electroplating process, inner layer pre-treatment, green oil pre-treatment, OSP treatment and other production lines, direct electrolysis has damage to the anode coating.
Etching solution
In the electronic circuit board (PCB) etching process, the copper content in the etching solution gradually increases. Etching solution to achieve the best etching effect, each liter of etching solution needs to contain 120 to 180 grams of copper and the corresponding amount of etching salt (NH4CI) and ammonia (NH3). The etchant regeneration cycle system has acidic and alkaline, and the two systems can be divided into extraction method and direct electrolysis method. It can reduce and regenerate a large amount of used etchant that originally needs to be discharged into regenerated etchant that can be used again. This can reduce the discharge of production waste liquid, reuse to reduce production costs, and can extract high purity electrolytic copper metal.
Advantages.
1, the use of iridium-tantalum coating, low relative oxygen overpotential, anode precipitation of oxygen, the anode is not subject to electrolyte corrosion.
2, high catalytic activity and stable chemical properties.
3, low initial voltage, low energy consumption.
Applications:
Alkaline etchant to recover copper
Acid etchant to recover copper
Microetching solution to recover copper
Titanium anode recycling copper process:
Quality checks:
Accelerated Life Test, Coating Thickness Test, Coating composition test,Conduct electricity conductivity testing,
Surface roughness test, Helium Leak Detection Test, Contact Resistance Test, Electrochemical Performance Test and other test.
JOINTING R&D
Improving current efficiency and prolonging service life are the core technical indicators of DSA titanium electrodes. Different industries have different requirements for the performance of titanium electrodes. Even if the same industry uses the same system of electrocatalytic coatings for different electrolytes, it may not be possible. Bring the ideal use effect. Based on years of accumulated R&D and production experience and a high-level technical team, the company can tailor a coating system that meets its own production environment for target customers to meet the differentiated needs of different industries or different customers in the same industry.
Development of electrode materials for high chlorine evolution efficiency and long life. Development of electrode materials for high acidity and long life oxygen evolution. Development of new electrode materials for mixed acid systems.
Development of high-oxygen ultra-base metal electrode materials Development of electrode materials in special fields