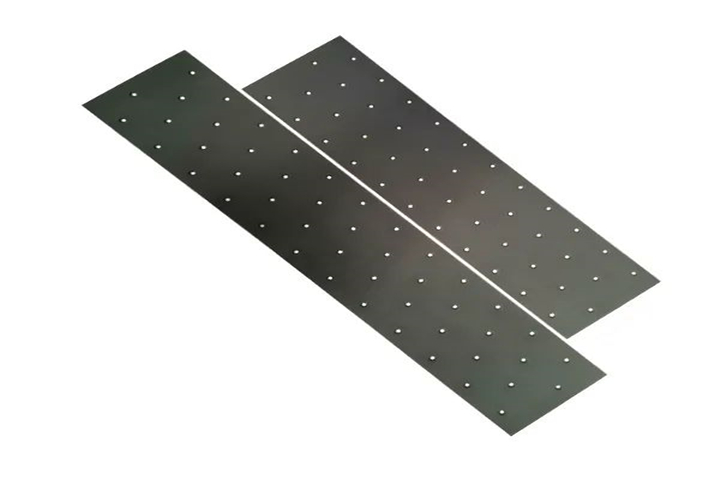
Electrolytic Foil Titanium Anode
Substrate: Titanium Grade 1 Sheet
Coating: Ir-ITa-X
The use of precious metal-coated titanium anodes as the preferred anode for the electrolytic copper foil industry has the advantages of low overpotential, stable pole spacing, and higher energy conversion efficiency, which not only reduces the tank voltage and power consumption but also avoids the electrolytic oxidation decomposition of organic substances such as amines in the copper foil manufacturing solution that occurs when lead electrodes are used, thus extending the life of the electrolyte and increasing productivity. It has an advantage over the conventional lead anode that is commonly used.
There are currently 2 types of raw foil machines on the market for anode plate processing, one is inlay type (1mm plum hole) and the other is back pull type (6mm FIP).
Copper foil titanium anode using industrial and mining conditions:
1、Electrolyte: Cu2+ >120g/L H2SO4>150g/L
2、Use temperature: <60℃
3、Use current density: 5000-8000A/m²
4、Chlorine content of electrolyte: <70ppm
5、The content of organic matter in the electrolyte: <25ppm
6、Pb2+ in electrolyte<35ppm
7、Service life: 8 months
Technical parameters and product advantages of our coated titanium anode:
1、Substrate material: TA1
2、Uniformity: sandblasting and acid etching are used, followed by ultrasonic cleaning.
3, coating structure: TA1 + composite intermediate layer + nano-coated iridium-tantalum mixture
4, electrocatalytic activity: increase the actual catalytic area of the coating by increasing the microscopic roughness of the titanium substrate. Add some base metal oxides to regulate the electrochemical performance of the electrode itself. Reduce the tank voltage and save energy.
5、Processing type: inlay type and back-draw type (curved plate)
6、Tolerable current density: <10000A/m²
7、Service life: 40000KAH/m2 (or 8 months), through a special sintering process to reduce and restrain the cracking of the coating surface, inhibit the erosion of solution oxygen and slow down the generation of TiO2 passivation film. The anode life is extended.
8、Re-coating of failed anode plate: Meanwhile, the biggest advantage of titanium anode plate can be repeatedly recoated (mainly for 6mm back-drawn FIP anode plate).
Application areas of electrolytic copper foil anode plate:
As one of the basic materials for the electronics industry, electrolytic copper foil anode plate is mainly used for manufacturing printed circuit boards (PCB) and lithium-ion batteries, which are widely used in home appliances, communications, computing (3C), new energy and other industries. In recent years, with the development of the 5G and the lithium battery industry, the requirements for copper foil are getting higher and higher. ultra-low profile copper foil for 5G and ultra-thin copper foil for lithium batteries have become the new development direction of copper foil technology.
Quality checks:
Accelerated Life Test, Coating Thickness Test, Coating composition test, Conduct electricity conductivity testing,
Surface roughness test, Helium Leak Detection Test, Contact Resistance Test, Electrochemical Performance Test, and other tests.
JOINTING R&D
Improving current efficiency and prolonging service life are the core technical indicators of DSA titanium electrodes. Different industries have different requirements for the performance of titanium electrodes. Even if the same industry uses the same system of electrocatalytic coatings for different electrolytes, it may not be possible. Bring the ideal use effect. Based on years of accumulated R&D and production experience and a high-level technical team, the company can tailor a coating system that meets its own production environment for target customers to meet the differentiated needs of different industries or different customers in the same industry.
Development of electrode materials for high chlorine evolution efficiency and long life. Development of electrode materials for high acidity and long life oxygen evolution. Development of new electrode materials for mixed acid systems.
Development of high-oxygen ultra-base metal electrode materials Development of electrode materials in special fields